3D-printed homes have been hitting the market. One company, Mighty Buildings, can 3D print structures twice as fast with 95 percent fewer labor hours and 10 times less waste than conventional construction. Started in 2017, the construction technology company spent a few years in “stealth” mode proving out its technology and working with compliance and regulatory agencies to develop future-forward materials that are tested to the most rigorous standards, before announcing itself publicly in August 2020. Since 2017, Mighty Buildings has grown to over 100 employees and has raised $100 million from leading investors including Khosla Ventures and Arctern Ventures.
I recently visited the Mighty Buildings facility in Oakland, where I spoke with Sam Ruben, chief sustainability and partnerships officer and co-founder at the company, about its work, his career journey and why sustainability is at the center.
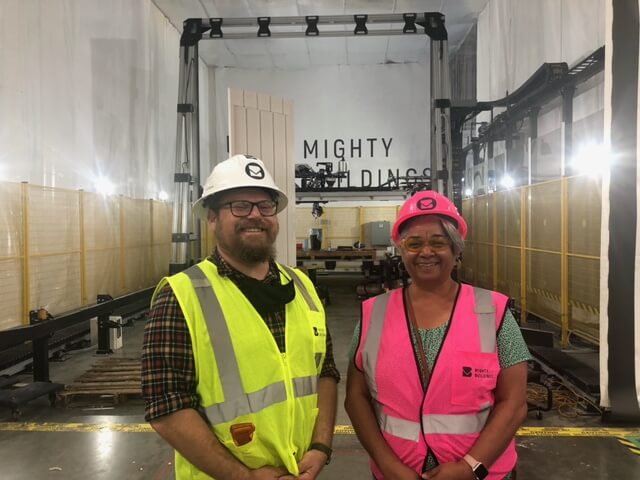
Ruben is an MBA/MPA graduate of the Presidio Graduate School (PGS) and was actually introduced to the other three co-founders of Mighty Buildings through a fellow PGS alumnus. Prior to Mighty Buildings, Ruben spent his career as a sustainability consultant, an EDF Climate Corps Fellows, and a community builder with the United Religions Initiative.
Below is a transcript of our conversation, lightly edited for clarity.
Cecily Joseph: Tell me about Mighty Buildings.
Sam Ruben: We’re an Oakland-based construction technology startup that is delivering sustainable housing built with unique 3D printing technology. I, along with my three co-founders — CEO Slava Solonitsyn, COO Alexey Dubov, and CTO Dmitry Starodubstev — bring a diverse set of backgrounds that has allowed us to approach the housing and climate crises with a unique perspective in order to help unlock productivity in construction while addressing the climate implications of that additional housing.
Joseph: Describe your role as its chief sustainability officer. How is Mighty Buildings different with its focus on sustainability?
Ruben: For me, it really is a dream job and one where I get to use both my degrees (MBA/MPA) from Presidio Graduate School on a daily basis. Along with leading our sustainability efforts, which includes working with my team to build out our roadmap to achieving carbon neutrality by 2028 ideally without offsets, I oversee our certification efforts (including our work with UL in creating the world’s first standard for 3D printed construction which underlies Appendix AW of the 2021 International Residential Code update, our work with ASTM leading their work on new standards for the application of additive manufacturing to construction, and our work with California Housing and Community Development’s Factory Built Housing Program), lead many of our external partnership efforts (such as our involvement with the Advanced Building Construction Collaborative, the Housing Innovation Alliance, and others), and serve as our primary spokesperson for media interviews. I really appreciate the diversity of areas I work in as I am a systems thinker and so it helps me have an expansive view of the ecosystem that is Mighty Buildings and more importantly the various systems that we interact with.
When choosing a title it was important to me personally, and us as a company, that it be chief sustainability officer. This is one of the ways that we have planted our flag in terms of the central importance that sustainability (and even more so resilience and regeneration) is to our core mission. We believe in approaching the housing and climate crises as a both-and proposition (or a “dual crises”) given the interplay between the two. The reality is that the climate crisis is more impacting the built environment and driving people from their homes — whether it be due to rising sea levels, increasing number and severity of wildfires, increasingly severe storm seasons, or even catastrophic wind events. And the housing crisis is placing more people in the face of these realities as housing costs drive construction farther away from city centers. And it is often those least able to afford it who face the brunt of these realities.
The lack of efficiency in the construction sector is on track to leave over 1.5 billion people, 1 in 3 urban dwellers, facing housing scarcity by 2025.
I think that approach and the fact that we are seeking to create revolutionary new ways of building rather than incremental changes to existing technologies makes our approach different. Not to say that there aren’t other amazing companies out there taking a similar approach, but no one is doing it quite like we are in terms of the technology that we are bringing to bear on the dual housing/climate crises.
Joseph: What are some of the biggest challenges facing the construction industry?
Ruben: There are challenges facing the construction industry on a variety of fronts. One of the biggest is the lack of productivity, which is a major factor in the housing crisis. According to McKinsey, the lack of efficiency in the sector is on track to leave over 1.5 billion people, one in three urban dwellers, facing housing scarcity by 2025. Additionally, from a business perspective, the construction industry is leaving $1.7 trillion on the table every year in unrealized revenue due to the lack of production.
Additionally, particularly here in the U.S., we are facing a labor shortage with around 400,000 jobs available in construction that aren’t being filled and an aging workforce that is retiring and not being replaced as young people go into the gig economy, programming or other roles who would have seen themselves in construction in previous years.
At the same time, construction of buildings accounts for 11 percent of all global emissions, and building energy use is around 30 percent. This means that even if we find the workers necessary to build all the homes we need using traditional methods, doing so will feed the climate crisis such that we might have enough homes but not in a world fit for humans to survive, much less thrive.
All of this points to the fact that we need better ways to build that increase efficiency, turn housing into a tool to fight the climate crisis, and attract a new generation of workers into the construction industry.
Joseph: How can 3D printing and other technologies disrupt the construction industry? Could it have an impact on underserved communities and/or address the affordable housing shortage in general?
Ruben: Obviously I’m biased, but I truly think that 3D printing has a chance to completely change how we approach the built environment and solve some of construction’s challenges in a way that few if any other technologies can.
The reality is that the industry largely still relies on the same technologies, or variations thereof, which we have been using for over 100 years (and in some cases much longer). 3D printing provides a completely new toolset for approaching issues related to all aspects of the design/build process — providing new pathways to unlock architect/engineer creativity while maintaining cost-effectiveness; solutions that can maximize the value of the human touch and create a safer working environment; opportunities to eliminate waste and reduce the amount of material needed to create buildings; and so much more, we truly are just scratching the surface.
Along with productivity and design freedom, there is also a significant opportunity to improve the lives and housing for marginalized and impoverished communities who, as noted above, often face the brunt of the climate crisis as well as the housing crisis. The past few years have brought companies to the fore who are using 3D printing to help solve the homelessness crisis.
At Mighty Buildings, we have a slightly different approach. Our initial focus has been on the “missing middle,” those who work and serve in communities (nurses, firefighters, teachers, etc.) but in too many places (like the Bay Area) can’t afford to live in those same communities and who generally do not qualify for subsidized housing. As we continue to scale and introduce new housing solutions, such as the multi-story production system we are kicking off the design of, our plan is to become truly market agnostic in terms of being able to provide cost-effective, high-quality homes that people can be proud of, regardless of what their price point is.
One of the reasons that we have accomplished as much as we have in only 4 years of existence is that we are able to bring a beginner’s mind to what we do.
Joseph: What is the long-term vision for your company?
Ruben: Our long-term vision is to be a tool for industry, allowing existing builders/developers to build more.
A key part of this vision is a production-as-a-service platform that is product, market and design agnostic — in other words, our plan is to be able to take third-party designs and automatically convert them into a 3D printable system. To this end, we have already developed a Revit library to support our panel system and make it easy to create custom floor plans for builders/developers. We will continue to develop this to allow architects/designers to work directly with our technology from the beginning of the design process. On the production side, our vision is a distributed network of Mighty Factories around the country (and the world) that would be located in high-demand areas where we have builder/developer partners. Because of the unique nature of our technology we are able to set up in a small footprint, meaning that we can leverage idle warehouse space to locate our facilities near demand and labor to ensure that our products reflect the local realities (rather than exporting California construction costs) in order to provide both housing and jobs to those markets.
We are also developing a micro-factory concept as a part of this which is a modular system in which each individual production cell is a self-contained system incorporating all stages of our process, allowing us to right-size a factory for even the lower-volume markets.
Joseph: We got connected through the Mighty Buildings Advisory Council you’ve just created and launched. I am honored to have been asked to join and really appreciate how you have intentionally sought out people who have sustainability backgrounds. It’s a bit unusual. How did you decide to create this council? What are the goals for this council?
Ruben: I suppose it is unusual, which is too bad as for us it simply makes sense. One of the reasons that we have accomplished as much as we have in only four years of existence is that we are able to bring a beginner’s mind to what we do and see things from a different perspective. However, we are also humble enough to recognize that there is much that we don’t know and so from the very beginning have sought to identify gaps in our knowledge and tap the right people as advisers, employees and partners to help fill them and to leverage the incredible expertise that already exists in the industry.
This is a part of our broader approach which can be summed up simply as “disruption through collaboration.” While we are bringing brand new technology to the market we also know that there is amazing expertise out there which we need to be taking advantage of in order to truly address the intractable problems that we are working on.
For us, this meant that as we move down our roadmap to carbon neutrality (and beyond), that we had the right group of people to serve as thought partners in achieving our aggressive goals. In bringing this group of partners together it was important that they were not solely drawn from one area but represent a diverse cross-section of stakeholders and experts both in sustainability as well as its applications in housing, material science, policy, CSR and so forth.
We’re really excited to have such an incredible group helping us live into our efforts while bringing new perspectives that we may not have ourselves, better helping us to create truly systemic solutions.